October 5, 2021 - 5 minutes read
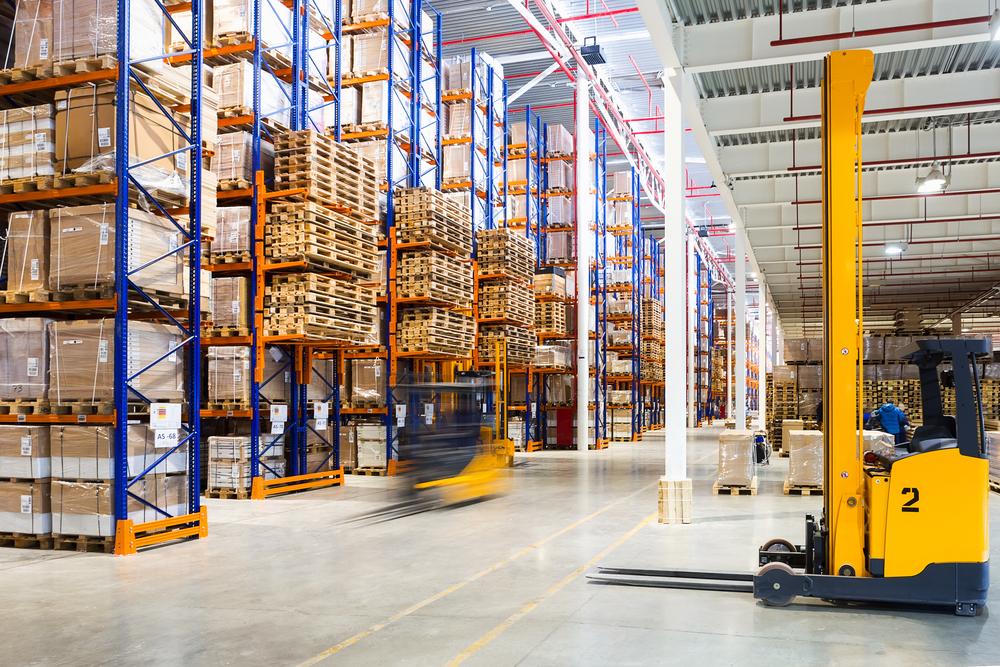
How to Accelerate Your Supply Chain With Micro-Warehousing
Warehousing is an essential component of any supply chain, regardless of the industry or region. Strong warehouse management execution is critical for a dependable pipeline to customers; an exemplary storage service is needed to support exemplary sales results. Furthermore, more efficient warehousing capabilities enable firms to acquire control of their inventory and effectively manage optimal global supply chain operations using innovative technology. It ultimately leads to client satisfaction.
As a result of increased digitalization, supply chains worldwide are under pressure to improve order fulfillment and more effectively utilize warehouse space.
Inventory anomalies have always been a costly problem, and companies are combating this problem through the automation of their warehouse operations.
What are micro warehousing and micro fulfillment? How can they improve supply chains?
Micro fulfillment, or micro warehousing, is a new trend in the supply chain industry. The concept of warehousing decentralization involves building a network of small fulfillment centers in strategically essential and dense areas to enhance last-mile deliveries and reduce transit times. Getting closer to the customers means establishing relatively small warehouses, in places such as retail malls, allowing for quicker delivery to clients, while also adding a self-pickup capability for customers to pick up their products locally.
Right now, the strategy is primarily used in e-commerce, the pharmaceutical business, and grocery distribution, but it’s becoming increasingly popular in other industries. A recent study by LogisticsIQ indicates that the micro fulfillment market will have a cumulative opportunity worth around $10b by 2026.
The concept of micro fulfillment creates a hub-and-spoke distribution strategy for businesses, with regional Delivery Centers (DC) acting as hubs and Micro Fulfillment Centers (MFCs) acting as spokes located near metropolitan population centers. Adopting the micro fulfillment strategy not only reduces the last-mile distance but also provides the option of in-store pickup fulfillment.
If the standard size of a warehouse facility is around 300,000 square feet, a typical micro-warehouse facility has a footprint of approximately 3,000 square feet. According to CB Insights, small fulfillment centers allow for the possibility of reducing overhead costs by 75% and providing greater agility. Since these facilities are smaller, they can be built relatively quickly and require fewer resources to manage and maintain. At the same time, customer satisfaction increases with reduced transit times.
The main drivers behind this trend are growing customer demands and growing delivery expectations. Regardless of the industry, end customers want faster deliveries and more convenient ways to collect products. Other factors contributing to the recent acceleration of micro fulfillment are intense digitalization, pandemic-driven supply chain disruptions, shrinking supply chain budgets, and sustainability concerns.
Micro warehousing is currently one of the best options for companies to compete with retail giants like Amazon and Walmart in terms of delivery times.
What are the other trends in warehousing and fulfillment?
Warehouse Automation
Keeping and maintaining warehouse facilities is expensive, and poor utilization can make warehouses even more expensive. Furthermore, warehouses are primarily supported by facility workers and their manual labor, accompanied by a great deal of paperwork that is impacted by human error. Using technology, such as robust WMS (warehouse management system) software, can assist with cutting labor costs, alleviating operational concerns, and improving the functioning of warehouses.
Dealing with many warehouse sites is a common challenge in complex global supply chains automation can help streamline the operations between internal, and external stakeholders, to keep all of your facilities connected and integrated.
Robotics
Robotic devices are another trend in warehouse and inventory management. Deploying innovative technology through robotic automation can drastically minimize manual activities, reduce the risk of human mistakes and increased labor costs, improve warehouse functionality, and optimize product arrival and distribution.
Retail behemoths like Amazon are already actively deploying robots alongside their human resources to improve operational efficiency. While it may appear that only Amazon size businesses can employ thousands of robots to optimize their warehouses, Deloitte’s 2019 Annual Industry Report states that more than 32% of supply chain professionals are already actively using robotics and automation for their warehouses, inventory, and fulfillment management.
Collaborative robots are also gaining popularity in warehouse automation. In fact, global sales of logistics management robots are expected to exceed $22.4 billion by 2021.
Sustainability
While sustainability has become an industry buzzword in recent years, it remains one of the most prominent themes and will continue to influence business in 2023. In the context of warehouse management, sustainable methods involve the use of renewable energy sources, such as solar batteries, and the recycling of packaging materials.
Energy prices, on average, account for 15% of general warehouse maintenance costs; therefore implementing a sustainable approach can be a strategic and profitable option.
Accelerating Global Supply Chains with Agistix
While micro-warehousing helps speed up delivery, it creates a few additional points in the supply chain. To truly achieve the expected result, companies need transparent tracking and data centralization at every step of the supply chain.
Agistix can help you tackle all of your supply chain challenges with a practical and proven visibility platform. Our key advantage is a seamless integration that requires no change to your regular business flow. After implementation, you will see results as soon as four weeks:
- Reduced costs
- Automated operations
- End-to-end visibility into any transaction and shipment
- Improved order fulfillment and inventory
- Reduced labor costs
- A proactive approach to detecting global supply chain gaps
We are familiar with the standard stumbling blocks in your supply chain. Because of our significant business experience, we can provide an easy-to-use software solution that puts control and visibility of your supply chain in the palm of your hand. Agistix’s solutions meet the needs of today’s rapidly expanding data interfaces and formats, allowing businesses to make non-disruptive and efficient changes to optimize their supply chains.
Learn more about Agistix’s sophisticated solutions here.